Friday, November 25, 2005
Construction of an F1 car
Design Office
The race-day performance of an F1 car has already been determined at the design stage. The design process is a path of evolution to enhance strengths and eliminate weaknesses, all with the goal of developing the finest F1 machine in the world.

Working under Keizo Takahashi, general manager of car design and development, Toyota's design department uses CATIA's state-of-the-art computer-aided design (CAD) software. An F1 car has about 3,500 separate elements, the majority of which have to be designed separately but must fit together with the utmost precision.
But long before any of the details have been designed, an F1 team determines the overall philosophy for their car. The team must balance potentially conflicting spatial requirements of the engine and gearbox, while the suspension and the aerodynamics must be reconciled into a package that is quick, but not unwieldy to actually produce and repair.
Although F1 cars must conform to a minimum weight limit of 600kg, the advantage of building the car underweight is that the engineers can optimize it to suit individual circuits by mounting ballast on different parts of the chassis.
Speeding up work with a lasersinter
The designers look to make many changes during the course of a season, whether to try out new aerodynamic parts or to accommodate changes to the engine or gearbox. A more powerful engine, for instance, will generate more heat, so the designers will have to improve heat dissipation - perhaps by installing larger radiators, or by finding more clever ways to vent the hot air aft of the radiators without impairing the aerodynamics. Designers also need to produce several variations of certain parts to suit specific circuits, including larger brake ducts for tracks that require heavy braking. Modern technology enables the designers to produce prototype parts easily, quickly and accurately. The composites department has a lasersinter machine that can produce high-quality parts in only a few hours. The lasersinter is a high-accuracy laser that selectively fuses together a polyamide powder to create the component. They do not have the structural strength of carbon fiber, but can be used in the wind tunnel or as molds for composite parts.
Chassis Construction
To achieve the highest standard of quality and consistency, Panasonic Toyota Racing uses the most sophisticated measuring equipment available. The machines in Toyota's CNC (Computerized Numerical Control) department can mill the smallest of components to an accuracy of four microns - about 25 times less than the width of a human hair - from a range of materials that include aluminum and magnesium. This is the sort of precision that F1 demands. As well as producing suspension and gearbox components, the CNC workshop makes the majority of the engine and many of the patterns that are used in the composites department to create the bodywork molds. In the composites department, the car as you recognize it begins to take shape.

Most structural composite components have an aluminum honeycomb core bonded with several layers of carbon fiber.
Step 1: Cutting A computer-controlled ultrasonic cutting machine slices precisely measured sheets of resin-impregnated carbon fiber cloth. Until it is cut, the carbon fiber has to be stored at - 18 °C, because it begins to harden at room temperature. An ultrasonic cutting machine is not a luxury- its speed and accuracy are vital. Some detailed cutting work is also performed by hand.
Step 2: Molding The cut sheets are laid into molds of predetermined patters in a special air-conditioned clean room. This pattern of interwoven matting is what gives the finished component its strength. The material is then put in a vacuum bag.
Step 3: Autoclave Once the parts have been put in a vacuum bag, they are moved to the autoclave. The autoclave is a sealed vessel that applies pressure (between two and six times normal atmospheric pressure) and heat. The pressure, combined with the vacuum bag, ensures that components fit the molds exactly, while the heat (usually between 130 and 140°C) hardens the resin. Since this process is computer controlled, the design team can change the programs as necessary.
Step 4: Assembly When finished, the parts are sent to the assembly division for finishing. Even parts formed to such precise specifications must be detailed by human hands to fit properly. This ensures that all parts can fit together properly. If drilling or other machining is required, the parts are sent back to the CNC division.
Engine Technology
Only two other F1 teams (Ferrari & Renault) constructs both its own engines and chassis. The close coordination between these two technical departments confers an advantage because it enables Panasonic Toyota Racing's designers and engineers to envision the car as a whole from the very first concept drawings. The word "drawing" is something of a misnomer, since the engines and chassis are designed on computers using CATIA CAD software. It takes around 1500 detailed "drawings" to make a complete engine.
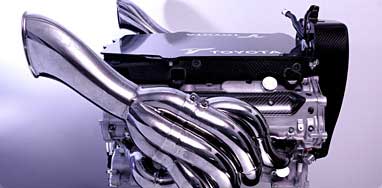
Luka Marmorini, General Manager of the Engine Division
"Our facilities are state-of-the-art. We have all the tools and people we need. We have hired some young engineers, some people from within F1, and we have people who have worked on Toyota's rally and Le Mans programs. It is a good mix of experience." Achieving the correct balance of performance, reliability and weight requires a methodical approach.
Exhaust pipes are created by hand. It takes one technician 50 hours to complete one pipe, and each pipe only has a life of one race.
The mechanics working in the engine workshop build and rebuild around 300 engines a year.The rebuilding process is not merely reassembly; around 40 percent of the 4,500 components will have to be replaced by new ones. All in all, it's a 200-hour job. The engine department has eight dynamometers that perform pre-race checks. These simulations use actual race data, which lets the engineers recreate realistic conditions for an engine without it ever leaving the factory.
Marmorini "Our goal is to make several performance leaps during a season. Of course, we cannot sacrifice reliability, which is why we take such pain-staking measures in production and testing."
Aerodynamics
Hilhorst's team has been working 16 hour days since Toyota's wind tunnel became operational in early 2002.
A wind tunnel experiment in progress
Toyota's wind tunnel is capable of simulating speeds in excess of 200mph on a half-scale model of a car. The steel belt "rolling road" accurately simulates the movement of a real road beneath the car - even though the car is stationary in the wind tunnel.
CFD Simulations Conducted First
Since minute changes can affect the flow of air across the entire surface of the car, the aerodynamicists must prioritize their ideas. Often they will use computational fluid dynamics (CFD) software to test the effectiveness of potential improvements before actually designing and making a new part. This not only saves money, it also minimizes the risk of spending days or weeks researching changes that do not result in an improvement.
Some aspects of a car's behavior are difficult to predict in software - pitch sensitivity, for instance, where the aerodynamics are adversely affected by the pitching of the car under acceleration and braking.
"CFD is useful," says a staff member, "but ultimately you must put your ideas to the test for real, either in the wind tunnel or out on track. If your preparation has been good, you will see the improvements."
The race-day performance of an F1 car has already been determined at the design stage. The design process is a path of evolution to enhance strengths and eliminate weaknesses, all with the goal of developing the finest F1 machine in the world.

Working under Keizo Takahashi, general manager of car design and development, Toyota's design department uses CATIA's state-of-the-art computer-aided design (CAD) software. An F1 car has about 3,500 separate elements, the majority of which have to be designed separately but must fit together with the utmost precision.
But long before any of the details have been designed, an F1 team determines the overall philosophy for their car. The team must balance potentially conflicting spatial requirements of the engine and gearbox, while the suspension and the aerodynamics must be reconciled into a package that is quick, but not unwieldy to actually produce and repair.
Although F1 cars must conform to a minimum weight limit of 600kg, the advantage of building the car underweight is that the engineers can optimize it to suit individual circuits by mounting ballast on different parts of the chassis.
Speeding up work with a lasersinter
The designers look to make many changes during the course of a season, whether to try out new aerodynamic parts or to accommodate changes to the engine or gearbox. A more powerful engine, for instance, will generate more heat, so the designers will have to improve heat dissipation - perhaps by installing larger radiators, or by finding more clever ways to vent the hot air aft of the radiators without impairing the aerodynamics. Designers also need to produce several variations of certain parts to suit specific circuits, including larger brake ducts for tracks that require heavy braking. Modern technology enables the designers to produce prototype parts easily, quickly and accurately. The composites department has a lasersinter machine that can produce high-quality parts in only a few hours. The lasersinter is a high-accuracy laser that selectively fuses together a polyamide powder to create the component. They do not have the structural strength of carbon fiber, but can be used in the wind tunnel or as molds for composite parts.
Chassis Construction
To achieve the highest standard of quality and consistency, Panasonic Toyota Racing uses the most sophisticated measuring equipment available. The machines in Toyota's CNC (Computerized Numerical Control) department can mill the smallest of components to an accuracy of four microns - about 25 times less than the width of a human hair - from a range of materials that include aluminum and magnesium. This is the sort of precision that F1 demands. As well as producing suspension and gearbox components, the CNC workshop makes the majority of the engine and many of the patterns that are used in the composites department to create the bodywork molds. In the composites department, the car as you recognize it begins to take shape.

Most structural composite components have an aluminum honeycomb core bonded with several layers of carbon fiber.
Step 1: Cutting A computer-controlled ultrasonic cutting machine slices precisely measured sheets of resin-impregnated carbon fiber cloth. Until it is cut, the carbon fiber has to be stored at - 18 °C, because it begins to harden at room temperature. An ultrasonic cutting machine is not a luxury- its speed and accuracy are vital. Some detailed cutting work is also performed by hand.
Step 2: Molding The cut sheets are laid into molds of predetermined patters in a special air-conditioned clean room. This pattern of interwoven matting is what gives the finished component its strength. The material is then put in a vacuum bag.

Step 4: Assembly When finished, the parts are sent to the assembly division for finishing. Even parts formed to such precise specifications must be detailed by human hands to fit properly. This ensures that all parts can fit together properly. If drilling or other machining is required, the parts are sent back to the CNC division.
Engine Technology
Only two other F1 teams (Ferrari & Renault) constructs both its own engines and chassis. The close coordination between these two technical departments confers an advantage because it enables Panasonic Toyota Racing's designers and engineers to envision the car as a whole from the very first concept drawings. The word "drawing" is something of a misnomer, since the engines and chassis are designed on computers using CATIA CAD software. It takes around 1500 detailed "drawings" to make a complete engine.
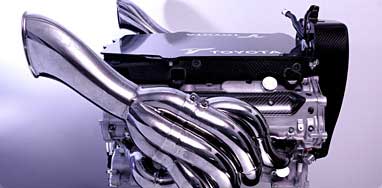
Luka Marmorini, General Manager of the Engine Division


The mechanics working in the engine workshop build and rebuild around 300 engines a year.The rebuilding process is not merely reassembly; around 40 percent of the 4,500 components will have to be replaced by new ones. All in all, it's a 200-hour job. The engine department has eight dynamometers that perform pre-race checks. These simulations use actual race data, which lets the engineers recreate realistic conditions for an engine without it ever leaving the factory.
Marmorini "Our goal is to make several performance leaps during a season. Of course, we cannot sacrifice reliability, which is why we take such pain-staking measures in production and testing."
Aerodynamics
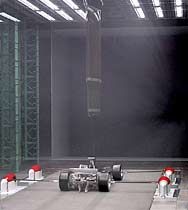
A wind tunnel experiment in progress
Toyota's wind tunnel is capable of simulating speeds in excess of 200mph on a half-scale model of a car. The steel belt "rolling road" accurately simulates the movement of a real road beneath the car - even though the car is stationary in the wind tunnel.
CFD Simulations Conducted First

Some aspects of a car's behavior are difficult to predict in software - pitch sensitivity, for instance, where the aerodynamics are adversely affected by the pitching of the car under acceleration and braking.
"CFD is useful," says a staff member, "but ultimately you must put your ideas to the test for real, either in the wind tunnel or out on track. If your preparation has been good, you will see the improvements."
Thanks to: Panasonic Toyota Racing
Comments:
Post a Comment